Begin Your Digital Transformation with These Four Free SOTI Snap Apps
- Dec 15, 2023
- 5 min read

SOTI Snap allows organizations to digitize manual processes and solves four problems associated with filling out pen-and-paper documents:
IT’S TIME-CONSUMING - It takes 40% longer to fill out a paper form than a digital form.
IT’S ERROR-PRONE - 25% of business revenue can be lost due to data inconsistency.
IT’S BAD FOR THE EARTH - It takes 30,000 cups of water to make 20,000 sheets of paper.
IT’S EXPENSIVE - Filing a single paper document costs $20 (USD).
Think about it. What’s faster: sending an email or mailing a letter? What’s easier: typing a search term to find a digital document or combing through endless file cabinets to locate one sheet of paper?
Going digital is the smart, efficient move, and that’s why 72% of organizations believe that business at the speed of paper – including manually filling and filing forms – will be unacceptable.
Four common pen-and-paper processes and/or forms organizations across all industries often seek to digitize include inspection forms, reporting forms, training forms and checklists.
Organizations can use SOTI Snap to quickly build these apps and deploy them to business-critical mobile devices. But, to help facilitate your digital transformation even faster, here are four pre-built, starter-level SOTI Snap apps from the SOTI Marketplace which are ready for you to access, edit and use.
The Forklift Inspection Checklist App
In industries such as transportation and logistics (T&L) and field services, forklifts are integral to productivity. They’re also complex pieces of machinery which are put under extreme duress.
When inspections aren’t carried out – or not documented properly – operators run the risk of getting behind the wheel of an unsafe piece of equipment that weighs an average of 9,000 lbs (4,082 kgs). Inspection violations can cost an organization over $13,000 (USD) with repeated offenses costing over ten times that amount at $132,000 (USD).
The average forklift inspection checklist takes around 5-15 minutes to complete, and the Forklift Inspection App ensures that any issues are captured correctly and shared quickly for immediate resolution.
While many government safety boards and forklift manufacturers recommend that forklifts be inspected prior to operation, poor documentation is still an issue. The Forklift Inspection App helps by featuring a graphical representation of a forklift with “hot spots” users can click to document issues.



The hot spots are mapped to areas of the forklift which suffer the most wear and tear:
Forks
Masts
Drive Tire
Steering Column
Fuel Tank
Additional hot spots can be added as required to areas such as the counterweight, the driver’s seat or steering tires. Users can take pictures to upload them to the app for perfect documentation whenever an issue is detected.
Pre-built fields include comments, location, forklift ID, supervisor name and inspected-by signature; more fields can be added to the app as necessary by IT staff and administrators with permissions to update SOTI Snap apps.
The Workplace Injury Reporting App
Worldwide, 340 million people suffer from workplace injuries. These injuries can range from common slips and falls to more serious trauma. Studies have shown that 69% of workplace injuries go unreported. Furthermore, approximately 70% of companies still use pen-and-paper processes to document and capture data associated with workplace health and safety.
When a workplace injury occurs, the priority after ensuring the well-being of the injured is to properly document the incident and the resulting injury. The Injury Reporting App allows organizations to collect and submit information related to a workplace injury quickly and easily.

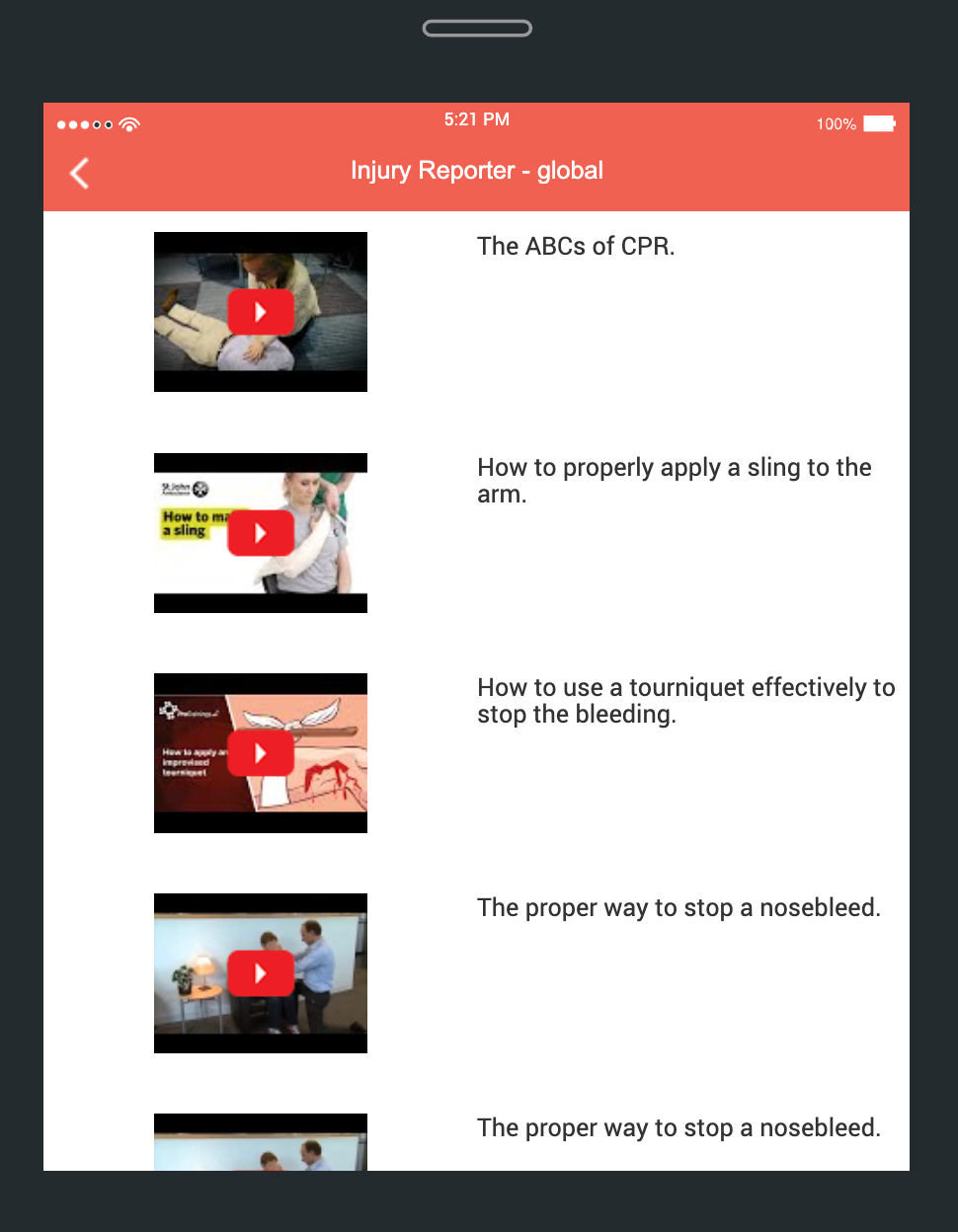
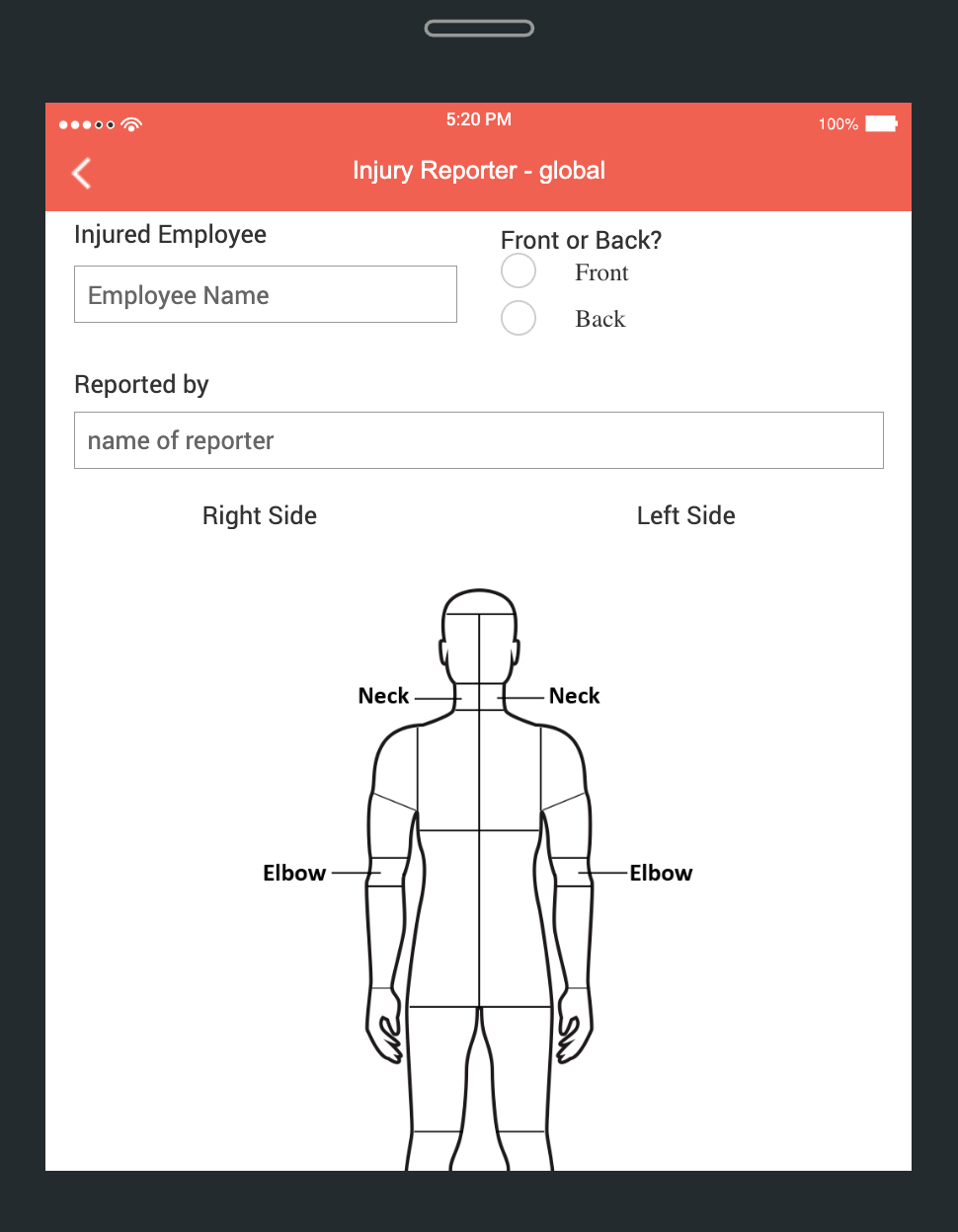
The best thing an organization can do after a workplace injury is take steps to prevent it from happening again. Using the built-in database of SOTI Snap, this empowers safety departments to record, archive and analyze reports to help improve safety.
Within the Injury Reporting App are fields to capture the name of the injured employee, where on the body the injury is, and a description of the industry. Additionally, there’s a representation of a human body with hot spots throughout (neck, head, shoulder, elbow, etc.). Clicking on a hot spot ensures complete accuracy regarding the location of the injury.
The Injury Reporting App also features a triage page with videos to help treat non-serious injuries which may occur in the workplace. These guided videos can help on-site workers provide first aid to injured employees. Videos can be added to or deleted from the Injury Reporting App as necessary. Rather than trying to look up this information when time is critical, the triage page in the app has it available and ready to go whenever it’s needed.
The Injury Reporting App helps organizations digitize manual reporting processes and ensure information is collected in a timely and accurate manner.
The Video Training App
Video-based training has proven to be effective as learning by video boosts recall and retention rates by 83%. One of the great benefits of video training is it can be deployed across any industry: retail, healthcare, emergency services – there really is no limit.
In addition to effectiveness, video training is quick and cost-efficient. It’s not uncommon for an organization to spend three weeks and significant funds on training initiatives. But with the Video Training App, organizations provide employees with a helpful tool to provide an engaging and impactful training experience.

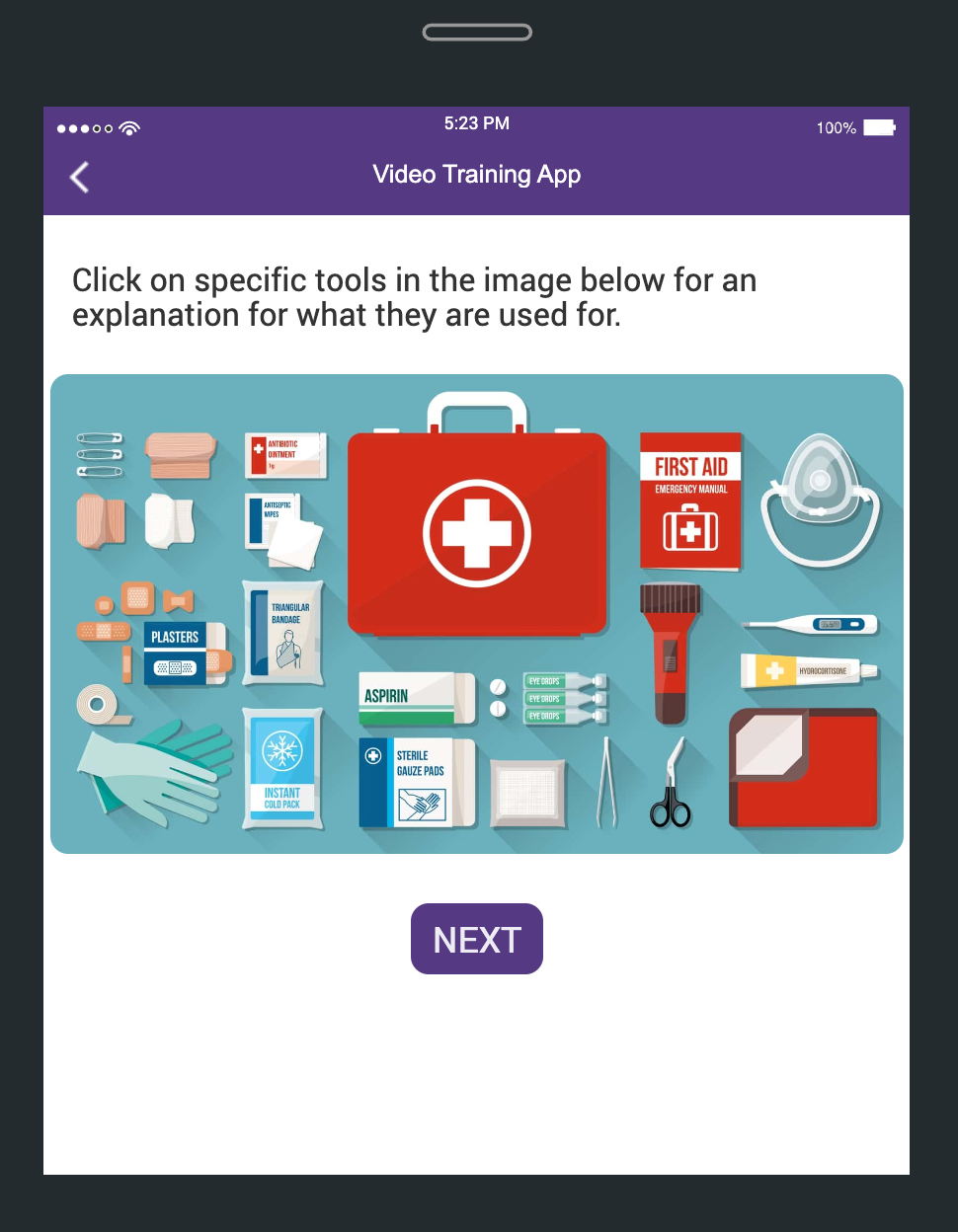
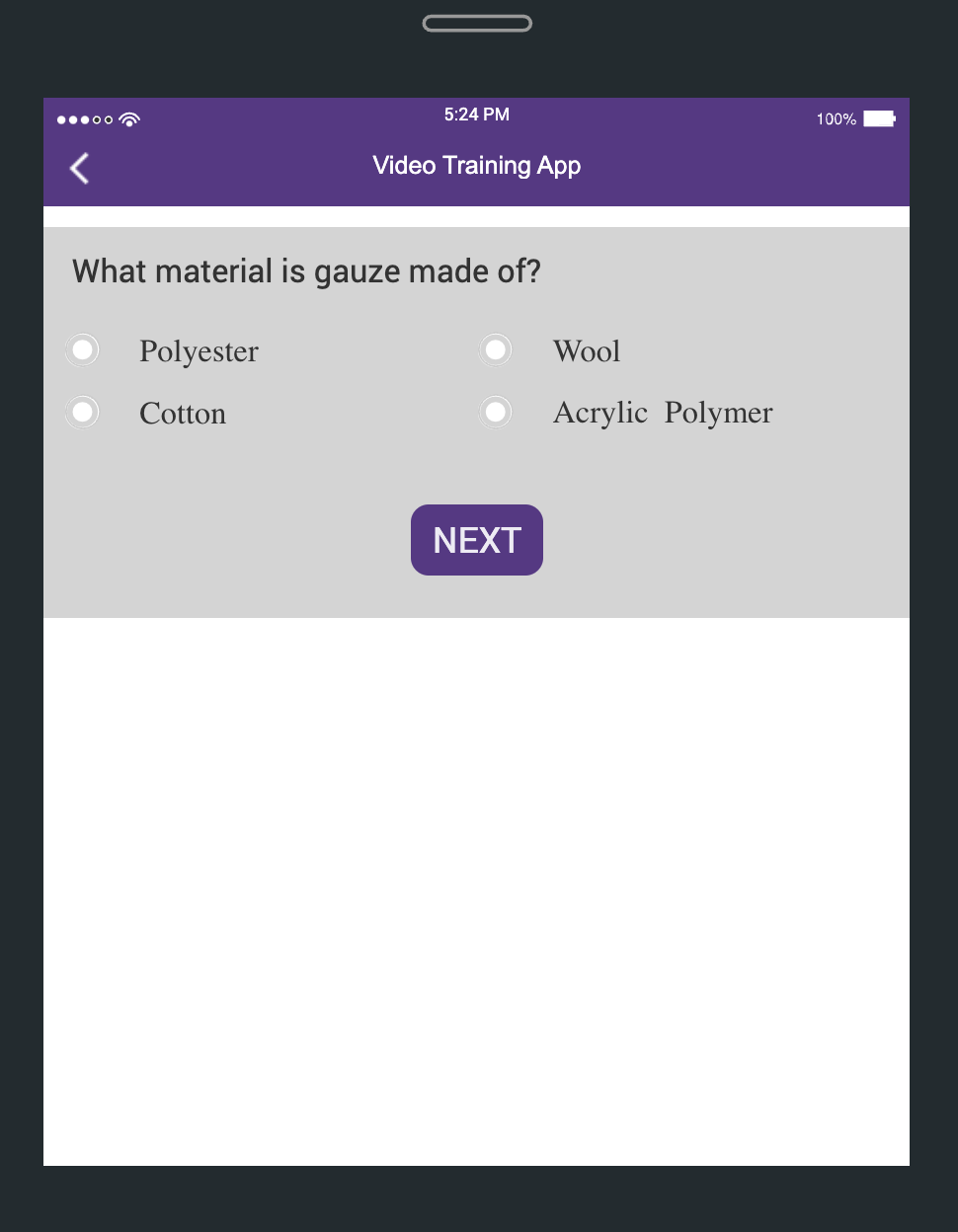
The Video Training App can host as many videos as required to facilitate a training session. Once the videos are viewed, the app prompts the user to take a quiz where they can demonstrate their knowledge via radio buttons for singular correct answers or checkboxes for questions with multiple correct answers.
Finally, the results of the quiz are displayed. If the user gets a passing grade, the training is complete. If the user does not, the app can instruct them to watch the video and take the quiz again. The app also features a study guide to help users better understand and apply the training they receive. Pass or fail results can be tracked, and the organization can be confident that training is complete and knowledge has been passed on when a passing mark is obtained.
With the Video Training App, organizations can develop videos featuring their own subject matter experts (SMEs) and deploy them to employees globally. It’s easier, faster and more scalable than trying to bring employees to a central location for in-person training. And as more video training is required, those videos can simply be added to the Video Training App whenever they’re ready.
The Store Opening Checklist App
When opening a retail store for the day, there are numerous steps which need to be taken: a security and safety inspection, checking the condition of the store for cleanliness, inventory and cash float counts, ensuring receipt printers have paper in them, etc. Missing a single step could ultimately lead to poor customer experiences.
Checklists have been proven to be powerful tools for improving productivity, effectiveness and efficiency. It also helps to have someone validate a checklist. The Store Opening Checklist App allows users to do both: it’s a step-by-step checklist to ensure all essential inspections are performed for a smooth store opening, and it uses SOTI Snap Workflow to send checklists to managers for approval or rejection.



The Store Opening Checklist App works in two parts. First is the checklist, which covers tasks such as a security and safety inspection. As the user moves from task to task, they can mark it as a pass or fail. Additional inspection tasks can be added to the checklist as required, and photos and extra information can be added to the checklist to provide more context. For example, if a floor sign fell overnight and became damaged, the user can take a picture of it and include it in the checklist.
The second part is the approval. Once the inspection checklist is complete, it can be sent to the manager for approval. The manager can review the checklist and approve it if it’s complete or reject it if any steps are missing or omitted. If the checklist is rejected, the manager can send it back to the submitter with instructions or comments to ensure it is properly completed and submitted.
Comentários